How Industrial Vibrators or Air Blasters Solve Material Flow Problems
Sometimes bulk material will not flow. Have you ever noticed how hard it is to get ketchup out of glass bottle, even when the bottle is held upside- down? Or have you ever seen a dump truck that remained full of the product it was hauling even after the bed was raised to the full dump position? These are examples of material flow problems. For decades, Industrial Vibrators and Air Blasters have helped restore flow to bulk solid materials. Let us explain how the use of vibration or sudden large blasts of air solve material flow problems. (Note: The terms bulk solid, bulk material, and material are used interchangeably. They all refer to the same thing - a form of particulate matter.)
What is a Bulk Solid (Bulk Material)?
A bulk solid is any non-fluid, particulate material which is usually handled in large amounts in unpackaged form. Bulk solids are frequently:
- Stored in hoppers, silos, or bins
- Shipped in railcars, self-unloading ships, bags, or trucks
Examples of typical bulk solids include:
- Kaolin Clay - used in ceramics, helps to strengthen and whiten paper, and used as a filler in rubber tires. It is shipped in powder form all over the world.
- Bauxite - an ore from which aluminum is made. It is crushed, washed, ground into powder and shipped to refining plants. It is mixed with clay to make bricks and is used by petroleum plants to deodorize and remove color from oils.
- Steel - steel requires numerous raw materials. For example, a steel mill requires iron ore from West Virginia, manganese from Brazil, fuel oil from Texas, scrap iron from Oklahoma, magnetite from Washington state, dolomite from Oregon, and ferrosilicon from New York. These bulk materials are typically transported in railcars.
- Sand or Gravel
- Cement
- Sulphur
- Lime
- Wood Chips or Sawdust
- Coal
- Coke
- Taconite
- Ashes - wet or dry
- Clay
- Rice - hulled
- Soap - flakes, powdered, chips
- Grain or Feed
- Pelletized or Granulated Materials for Manufacturing
- Limestone
- Salt, Flour, Sugar, or other types of food grade ingredients
- Solar Salt
- and thousands of others
Storage of Bulk Solids
Bulk Materials are stored in bins, hoppers, silos and other storage receptacles. These storage units are typically designed to empty under the influence of gravity. The chutes or discharge areas of typical bulk storage units feature smooth inner surfaces, with inclined walls, which allow the stored material to seek its lowest level and evacuate via the discharge opening. However, sometimes even gravity needs a little help.
Why do Bulk Solids have Flow Problems?
Bulk material flow may be affected by any combination of the following factors:
- Hopper design
- Moisture in the material causing stickiness or clinging
- Head or side pressure which compacts the material
- Friction between the material and the hopper walls
- Improper loading - material dumped onto existing material causing compaction
- A change in material density
Common flow problems are often categorized as:
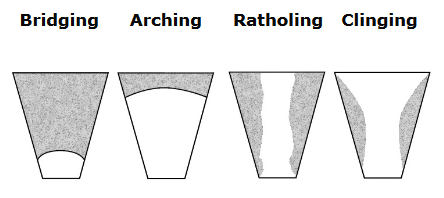
Solving Bulk Flow Problems ~ How Vibrators Work
Industrial Vibrators are the most common and effective way to solve bulk flow problems and restore material flow. The vibrator is designed to vibrate the material inside the storage vessel (bin, hopper, etc), not to violently shake the hopper. A well selected and properly mounted vibrator will restore flow causing no damage to the storage vessel (an oversized and improperly mounted industrial vibrator can damage a structure). As the material vibrates, it is displaced from the hopper wall reducing the friction between the material and the wall. This allows gravity to pull the material downward to restore flow.
There are two basic types of industrial vibrators, which are classified by the type of vibratory force they produce. The properties of the vibrational force and frequency they produce are quite different from each other and are used for different applications.
Two Basic Types Of Industrial Vibrators:
- Linear Vibrators
- Rotary Vibrators
Linear Vibrators are frequently referred to as piston vibrators because they use a reciprocating piston to produce an impact action that flexes the container wall. This flexing action loosens material stuck to the wall, thus restoring material flow.
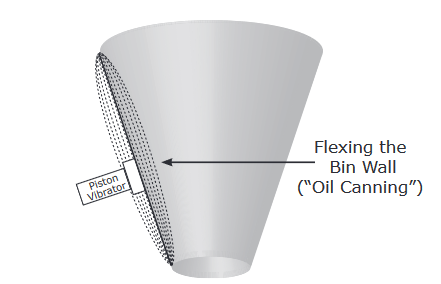
Principles of Linear Vibration
The "first" linear vibrator was a mallet or sledge hammer. Linear vibrators generate an impact action (shock wave) against the bin wall. The impact action causes the bin wall to flex back and forth, which is called "oil canning". The linear displacement of the bin wall loosens the bulk material, reducing the friction between the material and the bin wall, allowing the material to flow down the bin wall. In some cases the linear vibrator must generate a great amount of force to move the material, which creates excessive noise, and can cause structural damage if mounted improperly. An example of this was a chute, in a factory making powdered detergent. At the factory the detergent was transferred through several floors via a chute about 5 feet (1.5 m) in diameter, but there were flow problems because it clung to the sides of the chute wall. To solve the clinging problem, the factory installed a piston vibrator on the chute. They gradually had to increase the size of the piston vibrator because they could not get the product to flow properly. Eventually a 4" piston vibrator was installed, but it caused even more problems by damaging the chute and generating excessive noise. Sometimes the wrong type of industrial vibrator is selected to solve a flow problem, and when it does not solve the problem, it is replaced with a larger more forceful vibrator. Bigger is not always better. A piston vibrator was not the best solution for the detergent application. A rotary industrial vibrator replaced the piston vibrator and worked perfect.
Two general types of linear (piston) vibrators:
- Impacting Piston allows the internal piston to strike the base of the vibrator producing the greatest amount of force and frequency.
- Non-impacting (Air-Cushioned) Piston uses a cushion of air to dampen the piston movement, so the piston reverses directions before impacting the vibrator base. Therefore, air-cushioned pistons are more quiet, but also produces less force and frequency than impacting type.
Properties of Piston Vibrators:
- Pneumatic piston vibrators consume less air than pneumatic rotary vibrators.
- Produce back and forth motion needed by feeders and shaker screens.
- Pneumatic Piston vibrators work better than sledge hammers. Bashing the bin with a sledge hammer causes concavities inside the bin, which gives material a place to hang-up, causing more flow problems. The destruction by the sledge hammer can be avoided by using an industrial vibrator.
- Flexing may cause structural fatigue if proper mounting is not followed.
- Very noisy - impacting piston vibrators can produce 110 dB or more.
Examples of linear vibrators:
- Pneumatic Piston Vibrators
- Electromagnetic Vibrators
- Sledge Hammer
Rotary Vibrators create a sinusoidal wave of energy that behaves quite differently than linear vibration. Industrial rotary vibrators use a rotating unbalanced weight to produce this wave of energy. When the energy is harnessed by proper mounting, rotary vibration is transferred through the hopper wall to the material within the hopper. When the sinusoidal wave of energy is tuned to the material's natural resonant frequency, the bulk solid begins to flow like magic!
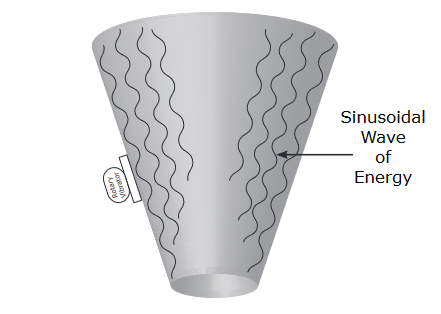
Principles Of Rotary Vibration
A rotary vibrator produces "rotary" vibration using a rotating, unbalanced weight (like a car tire not properly balanced). The weight is unbalanced because its center of gravity differs from its center of rotation. The unbalanced force or eccentricity, which creates the vibration, is dependent on the mass of the rotating weight. The unbalanced force is determined by the distance between the centers of gravity and rotation and is expressed in inch- pounds (kg-mm). For example, a weight of one pound with a center of gravity situated one inch from the center of rotation is said to have one inch- pound of unbalanced force.
The frequency is the number of full revolutions made by the rotating weight in a rotary vibrator over a period of time. Frequency in our specific industry is expressed in "rotations per minute" (rpm). Centrifugal force, expressed in force pounds, refers to the force developed by the rotating eccentric weight. The larger the unbalance weight is and the faster it rotates, the greater the centrifugal force produced. This force determines the amplitude of the rotary vibrator's energy wave.
Centrifugal Force Pounds Equation:
Unbalance (in-lb) x .0000284 x RPM² = Centrifugal Force Pounds
"Rotary" vibration is a sinusoidal wave of energy. The speed of rotation determines the frequency of vibration. The Centrifugal Force is the force generated by a rotating unbalanced weight and is represented by the amplitude (A) of the sinusoidal wave. This force, measured in force pounds, results from the tendency of a rotating mass to escape its orbit. It is applicable only to rotary vibrators (It is not the same force as the linear force produced in piston type vibrators).
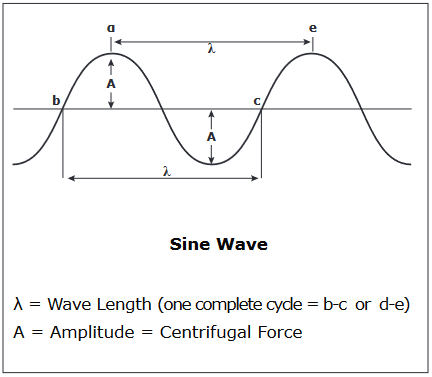
CENTRIFUGAL FORCE (CF) is proportional to:
- Weight of the rotating mass
- Eccentric distance (distance between the center of mass and center of rotation)
- Speed of rotation (cycles or rotations per minute) squared
Effects:
- Double the weight = double the centrifugal force
- Double the eccentric distance = double the centrifugal force
- Double the speed (rpm) = four times the centrifugal force
Properties:
- Non-impacting type of vibration has little effect on container wall
- Less noisy - due to no impacting or flexing of the bin wall
- Greater area-of-influence - When properly mounted the vibration can be transmitted to effectively energize more material than piston vibrators
- "Controlled" directional mass flow
- Discharges evenly, first in - first out
- Limited segregation of particles - helps in quality control of products such as potting soil & concrete
- When the frequency of vibration approaches the natural frequency of the material, less force is needed to vibrate and move the material - (Principle of Resonant Frequency)
Examples of rotary vibrators:
- Pneumatic Ball Vibrators
- Pneumatic Roller Vibrators
- Pneumatic Turbine Vibrators
- Air Motor Driven Vibrators
- Hydraulic Motor Driven Vibrators
- Electric Rotary Vibrators
What Is Resonant Frequency?
Particles of any type of material vibrate in response to applied energy. The amount of movement or amplitude of vibration is dramatically enhanced when the frequency of the applied energy matches the natural frequency of the material. When this occurs, the material is said to resonate. The natural or "resonant" frequency of a material is that frequency at which it will most easily vibrate (requires the least amount of energy to cause it to vibrate). A piano uses the unique natural frequency of its strings to make beautiful music. For instance, when the middle "C" piano key is played, we hear a "C" sound because the string which is "tuned" to resonate at 256 vibrations per second is struck. All the other strings begin to vibrate too, but only the middle "C" vibrates with enough amplitude to be heard. It is the only string vibrating at its resonant frequency.
Like all material, structures and bulk solids have specific resonant frequencies. The resonant frequency of a particular material depends greatly on the mass and geometrical characteristics of that material. The resonant frequency of a hopper wall will differ from the bulk solid contained inside, therefore the frequency of energy which causes the hopper to vibrate maximally is not the same frequency that "excites" the bulk solid. Typically the hopper walls resonate at low frequencies, while bulk solids resonate at higher frequencies.
Putting Engineered Vibration To Work
Applied vibration can be very useful in establishing bulk material flow. Rotary vibration causes displacement of the material away from the hopper wall, allowing the material to "slide" from the hopper. It reduces the friction between the hopper wall and the bulk material allowing gravity to do the rest of the job.
- Centrifugal force causes displacement of material
- Displacement reduces friction of material
- Material flows easily because of reduced friction and pull of gravity
Usually rotary vibrators with small unbalanced force are run at high RPM to produce high frequency / low force vibration. Vibrators with large unbalanced force are run at slower speeds to produce more force / lower frequency vibration.
When energy is applied to a bulk solid at its resonant frequency, a small amount of force can produce a large displacement of the material (the frequency of the force is synchronized with the natural frequency of the material). If the vibration hits somewhere on the resonant frequency curve of the bulk material, flow will occur. Knowing the 'exact' resonant frequency of the material is not necessary, and such a thing is difficult to know because the density of the material changes under different circumstances. There are general 'rules- of-thumb' to follow, which will help solve your flow problems. When energy is applied at a frequency other than the resonant frequency, a larger amount of force will be required to displace the same amount of material (frequency of the force is not synchronized with the natural frequency of the material).
Rotary vibrators can be "tuned" to get maximum performance. Vary the frequency of the vibration by adjusting the rpm of the hydraulic motor or the cfm of the pneumatic motor or vibrator. The general rule-of-thumb is to vary the speed (frequency which equals rpm) to match the conditions. An inverter can be used to adjust the speed of an electric vibrator. Also many of our industrial vibrators have adjustable weights, which give different unbalanced force ratings. Since materials resonate at their natural frequency, approximate that frequency by adjusting the rpm (speed) until the material flows. In general, fine, particulate material responds best to high frequency vibration, whereas coarse, heavier material responds best to more force and lower frequency. Some bulk solids, such as solar salt, require high frequency to excite the fine material, but also high force to move the mass because it is very wet and heavy.
General Guidelines for Bulk Material ~ Speed and Force Suggestions
- Amplitude Sensitive Materials are usually larger heavier materials such as coal, rock, and gravel and respond well to slower waves of energy of greater amplitude.
- Frequency Sensitive Materials are usually fine particulate materials such as salt, cement, and flour and respond well to faster waves of energy.
- Materials that are neither small in size or large, but are somewhat 'airy', such as, wood-chips respond better to slower waves of energy and usually need more force to establish flow even though the weight of the material is minimal. Another atypical bulk solid is solar salt. It needs high frequency because the product is made up of fine particulate, but it also needs a lot of force because it is heavy. The high force output moves the mass of the solar salt and the frequency excites the 'fine particulate (the salt)'. Turbine and Roller Vibrators have force and frequency necessary to solve these types of flow problems.